
On the other hand, the abundant presence of silica is judged to be very interesting and useful for a possible industrial exploitation. Because of its high content, the different extraction procedures of cellulose from RH 6,7 and rice straw 8 have been explored. RH main components are cellulose (38.3%), hemicellulose (31.6%), lignin (11.8%) and silica (18.3%), 5 respectively. In the present scenario, many researchers have focused their efforts on the possible uses of RH and RHA, considering their abundance and cheap cost as industrial wastes. 3 Indeed, during its combustion, about 20–25 wt% of rice husk ash (RHA), containing more than 90% silica, with traces of other metal oxides, is produced. Furthermore, it is well-known that RH can be also used as a renewable fuel in cogenerating plants, considering its high calorific value (4012 Kcal kg −1). 1 Although RH has been already employed in different fields (namely, as bio-fertilizer, as material for animal husbandry, as absorbent and building material or pest control agent 2), it is still often considered as a waste product of rice milling, and thus, often burned in open air or dumped on wasteland. The yearly global rice production has been estimated at 729 million tons for 2012, which implies more than 150 million tons of RH production, on the basis of the data published by the Food and Agriculture Organization (FAO) of the United Nations in the “Rice Market Monitor” report. Introduction Rice husk (RH) is an agricultural by-product abundantly available: indeed, its accounts is one out of five of the annual worldwide rice production. Finally, an economic analysis of material and energetic costs has been performed on samples containing silica from rice husk in order to establish if the proposed process is sustainable or advantageous.

Two micro-mechanical models (Voigt and Halpin–Tsai) have been used to also fit the mechanical data. The collected values at 10 and 30 wt% have been compared with those of homologous samples prepared using a commercial silica. Despite a broad distribution of silica particle size, the prepared bio-composites have exhibited improved storage modulus and reduced oxygen permeabilities. The thermal, mechanical and morphological properties have been investigated.
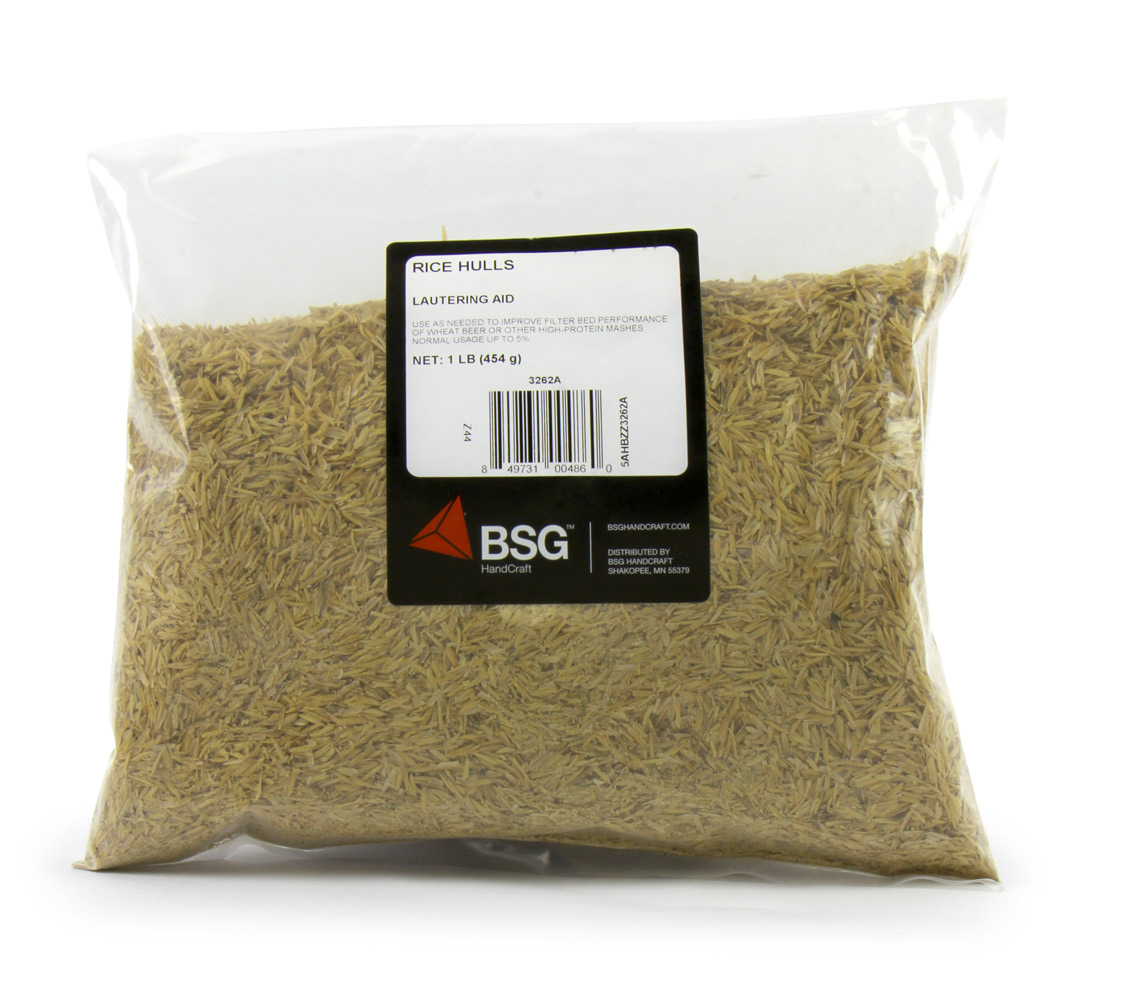
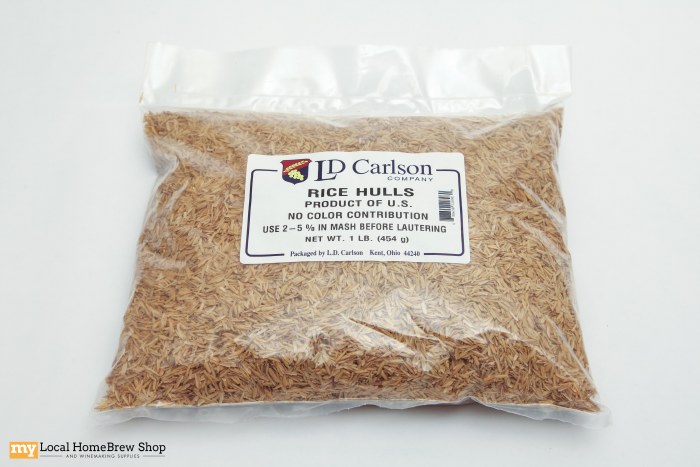
These materials have been obtained through a semi-industrial process of extrusion. Silica powder has been extracted from rice husk employing a simple extraction procedure for preparing poly(lactic acid) bio-composites with differing filler contents (namely, 5, 10, 20 and 30 wt%).
